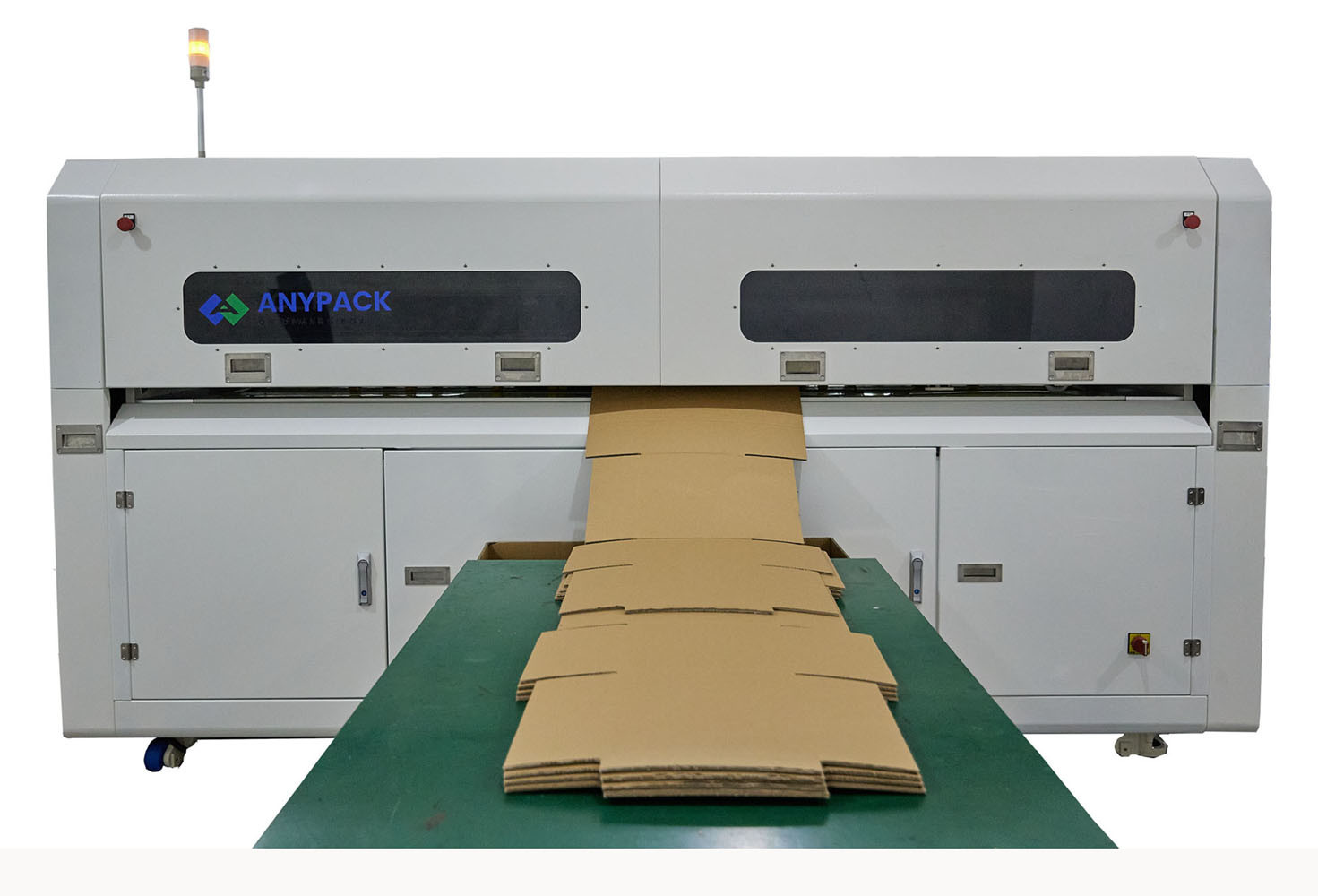
Engineering Efficiency: The Dynamics of Corrugated Box Machines
In the intricate web of industries that drive the global economy, packaging plays a pivotal role. Among the many packaging solutions available, corrugated boxes stand out as versatile, durable, and eco-friendly. Behind the scenes of these seemingly simple boxes, however, lies a complex world of engineering marvels – the Corrugated Box Machine. In this blog, we delve into the dynamics of these machines, exploring how they contribute to the efficiency of the packaging industry.
The Evolution of Corrugated Box Machines
The history of corrugated boxes dates back to the 19th century, but it wasn’t until the early 20th century that corrugated box machines began to emerge. The initial designs were rudimentary, requiring significant manual labor. However, as technology advanced, these machines evolved into sophisticated systems capable of high-speed production with minimal human intervention.
Structural Anatomy of Corrugated Box Machines
At the heart of these machines lies the corrugator, a colossal piece of engineering that orchestrates the entire process. The corrugator comprises several key components:
- Roll Stand: Unwinding rolls of paper, the roll stand feeds the raw material into the machine.
- Single Facer: This section corrugates the paper, creating the iconic wavy pattern that gives corrugated boxes their strength.
- Glue Unit: Responsible for applying adhesive to the corrugated medium, the glue unit ensures proper bonding between layers.
- Double Backer: This part combines the corrugated medium with the liner sheets, forming the triple-layer structure characteristic of corrugated boxes.
- Slitter Scorers and Cut-Off Knife: These components shape the corrugated board into the desired dimensions, ready for the conversion into boxes.
- Stacker: The final step involves stacking the finished sheets for further processing or packaging.
Automation and Efficiency
One of the most significant strides in the world of corrugated box machines has been the integration of automation. Modern machines are equipped with sensors, robotics, and computerized controls that optimize the entire production process. Automation not only reduces the margin of error but also enhances speed and efficiency, leading to higher output levels.
Customization and Flexibility
Corrugated box machines are designed to accommodate a wide range of box sizes and styles. Whether it’s a small shipping box or a large packaging container, these machines can be adjusted to meet diverse industry needs. The ability to customize box dimensions and styles adds a layer of flexibility that is crucial for industries with varying packaging requirements.
Environmental Sustainability
In an era where sustainability is a top priority, corrugated box machines play a role in promoting eco-friendly practices. Corrugated boxes are recyclable and made from renewable resources, aligning with the global push towards a greener future. The efficiency of these machines ensures that the production process is streamlined, reducing waste and resource consumption.
Challenges and Innovations
Despite their efficiency, corrugated box machines face challenges such as maintenance, technological obsolescence, and adapting to rapidly changing market demands. However, the industry responds with continual innovations, introducing features like predictive maintenance algorithms, remote monitoring, and modular designs that facilitate upgrades.